Our high voltage coils are manufactured in-house and we offer a range of resin rich and global VPI insulation systems for industrial, power generation and specialist applications. With absolute control over quality, we manufacture stator, armature, field and rotor coils for all types of motors and generators up to 15kV, in diamond and concentric designs.
With over 30 years multi industry experience in electro mechanical engineering we offer:
- Supply and manufacture of premium high voltage coils and auxiliary winding kits
- Fully tested with a 5 year warranty
- Specialist electro mechanical engineering support
- Computer aided design, performance upgrade and reverse engineering capabilities
- Worldwide in situ support services
- ISO certified manufacturing facility with state of the art coil press
We currently export to over 30 countries worldwide, including Canada, Greece, Hong Kong, Indonesia, Australia, Nigeria, Norway, Venezuela, Malaysia, the Middle East, the USA and the Caribbean.
Customers are kept up to date using video communication which offers live work in progress updates, visual diagnostic reports and live test results via video link to all them to keep track of their HV coils wherever they are in the world.
All full data quotes are presented using our AutoCoil design software, utilising the latest technology to offer 3D coil design and slot build drawings for improved design and accurate fit.
Using our extensive manufacturing expertise, we have developed a comprehensive range of insulation systems suitable for all applications, including –
- HiFLEX™ Our innovative, fully tested, totally flexible insulation system.
- HiRES™ Our B-stage end winding solution
- HiBRID™ Our unique insulation system combining the merits of Vacuum Pressure Impregnation (VPI) and resin rich technology
- HiVAX™ Our VPI insulation system
We are also experienced in the manufacture of half bar systems, which are used in the winding of turbo generator machines up to 70MW.
To learn more about Houghton International, specialist high voltage coil manufacturers, contact us today. You can find more information on our website about our range of other services, including rail traction motor services and electric motor rewind services.
Further Information
Range of insulation systems
Related Services


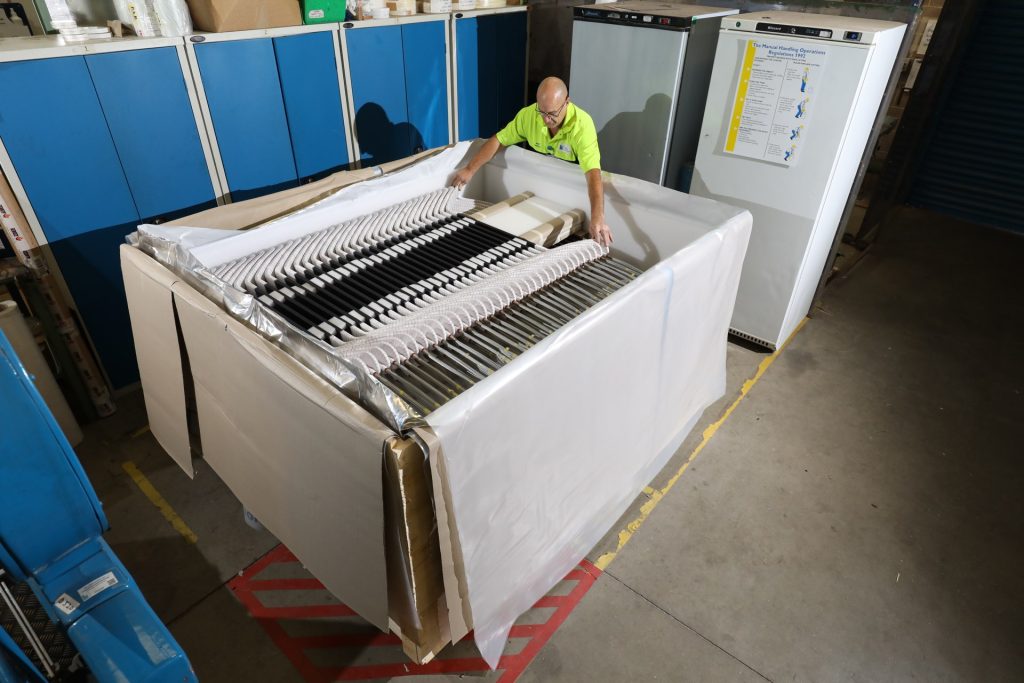



Contact us for more information on our high voltage coils
Get in touch using the boxes below and we’ll get back to you.